Self-lubricating bronze bushings are widely used in industrial applications due to their durability, low maintenance, and ability to operate in harsh conditions. Unlike traditional bushings that require constant lubrication, these components are embedded with solid lubricants, reducing friction and wear over time.
Self-lubricating bronze bushings are engineered to provide long-lasting performance without the need for frequent oil or grease replenishment. Their unique design makes them ideal for applications where maintenance access is limited or where contamination from external lubricants must be avoided.
Key Benefits
Reduced Maintenance: No need for constant relubrication, lowering downtime.
High Load Capacity: Can withstand heavy loads and shock impacts.
Corrosion Resistance: Performs well in wet or chemically aggressive environments.
Wide Temperature Range: Suitable for both high-heat and cryogenic applications.
Common Applications
Heavy machinery (excavators, cranes)
Marine equipment (propeller shafts, rudder bearings)
Automotive suspensions and steering systems
Food processing and pharmaceutical machinery (where oil contamination is a concern)
Maintenance Tips
Inspect Regularly: Check for wear or embedded debris.
Clean When Necessary: Use non-abrasive methods to avoid damaging the self-lubricating layer.
Avoid Overloading: Ensure the bushing operates within its rated capacity.
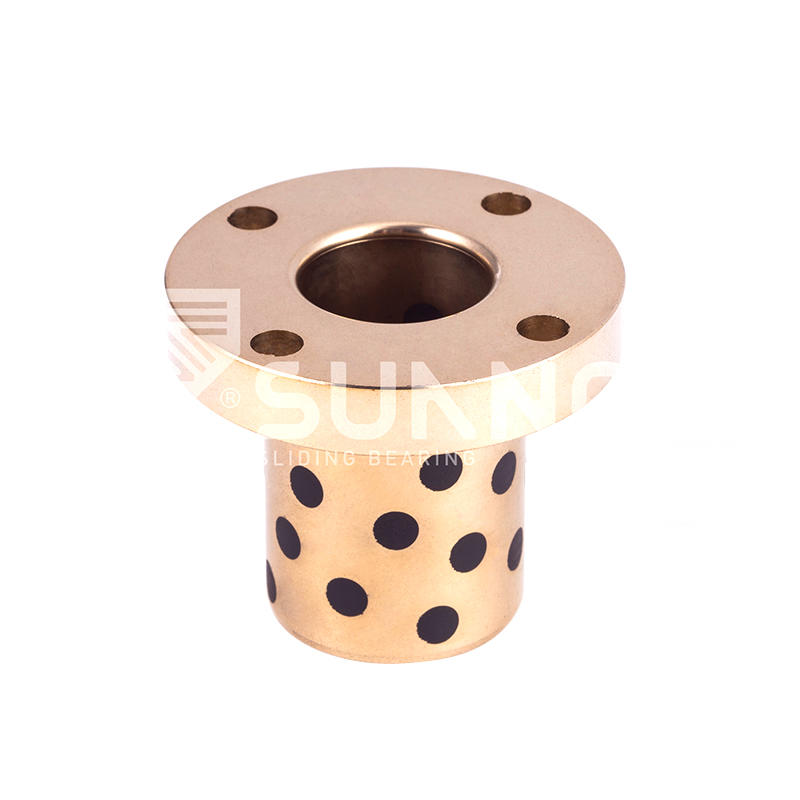
JFB650 Metric Oil Free Self Lubricating Bronze Round Flanged Bearing
2. How Self-Lubricating Bronze Bushings Reduce Maintenance Costs in Heavy Machinery
Heavy machinery operates under extreme conditions, making lubrication a critical factor in preventing wear and failure. Self-lubricating bronze bushings significantly cut maintenance expenses by eliminating the need for frequent lubrication.
Cost-Saving Advantages
Fewer Lubrication Intervals – No need for manual greasing, reducing labor costs.
Extended Service Life – Less wear means fewer replacements.
Lower Downtime – Machines run longer without maintenance stops.
Reduced Contamination Risk – No oil leaks that could damage other components.
Case Study: Mining Equipment
In mining applications, where dust and debris are common, traditional bushings fail quickly due to grit contamination. Self-lubricating bronze bushings last longer because their embedded lubricants are protected within the material structure.
Best Practices for Heavy Machinery
Choose bushings with high graphite content for better dry lubrication.
Ensure proper alignment and installation to prevent uneven wear.
Monitor for abnormal noise or vibration, which may indicate wear.
3. Self-Lubricating vs. Oil-Lubricated Bronze Bushings: Which Is Right for Your Application?
Choosing between self-lubricating and oil-lubricated bronze bushings depends on operating conditions, maintenance capabilities, and performance requirements. This section compares both types to help you make an informed decision.
Comparison Table
Feature |
Self-Lubricating Bronze Bushings |
Oil-Lubricated Bronze Bushings |
Lubrication Needed |
No (embedded lubricants) |
Yes (external oil/grease) |
Maintenance |
Low |
High (frequent relubrication) |
Load Capacity |
High |
Moderate (depends on lubrication) |
Environmental Suitability |
Works in dirty/wet conditions |
Requires clean conditions |
Cost Over Time |
Lower (less maintenance) |
Higher (more servicing) |
When to Choose Self-Lubricating Bushings
Harsh Environments (dust, water, chemicals)
Maintenance-Free Needs (sealed or hard-to-reach areas)
Long-Term Cost Efficiency
When to Choose Oil-Lubricated Bushings
High-Speed Applications (where oil films reduce friction better)
Precision Machinery (where controlled lubrication is critical)
Short-Term Cost Savings (if initial budget is a constraint)
Final Recommendation
For most industrial applications, self-lubricating bronze bushings provide better long-term value due to their durability and reduced maintenance. However, oil-lubricated versions may still be preferred in high-speed or precision systems where continuous lubrication is manageable.