In the realm of mechanical engineering, bearings are fundamental components that enable smooth and efficient motion. Among the myriad of bearing types, SF-1 oilless bearings have emerged as a revolutionary solution, offering exceptional performance without the need for external lubrication. This article delves into the intricacies of SF-1 bearings, exploring their composition, benefits, applications, and crucial considerations for their selection, installation, and maintenance.
1. Materials and Manufacturing Process of SF-1 Oilless Bearing
SF-1 oilless bearings are a testament to advanced material science and engineering. Their unique properties stem from a sophisticated multi-layered structure:
Base Material (Steel Back): The foundation of the SF-1 bearing is typically a low-carbon steel back. This robust layer provides the necessary mechanical strength and rigidity to support heavy loads and ensure structural integrity. In some specialized applications, a bronze back may be used for enhanced corrosion resistance or thermal conductivity.
Porous Bronze Sintered Layer: Bonded to the steel back is a layer of porous bronze powder, usually sintered. This porous structure is crucial as it acts as a reservoir for the self-lubricating material. The interconnected pores ensure an even distribution of the lubricant.
Self-Lubricating Layer (PTFE/Filler Composite): The innermost layer, and the key to the SF-1 bearing's "oilless" characteristic, is a composite material impregnated into the porous bronze. This layer primarily consists of Polytetrafluoroethylene (PTFE), a material renowned for its extremely low coefficient of friction and excellent chemical inertness. To enhance wear resistance and thermal conductivity, various fillers are strategically blended with the PTFE. Common fillers include lead (though its use is decreasing due to environmental concerns), copper powder, graphite, and other proprietary solid lubricants. These fillers work synergistically with PTFE to provide continuous lubrication, even under high pressures and varying temperatures.
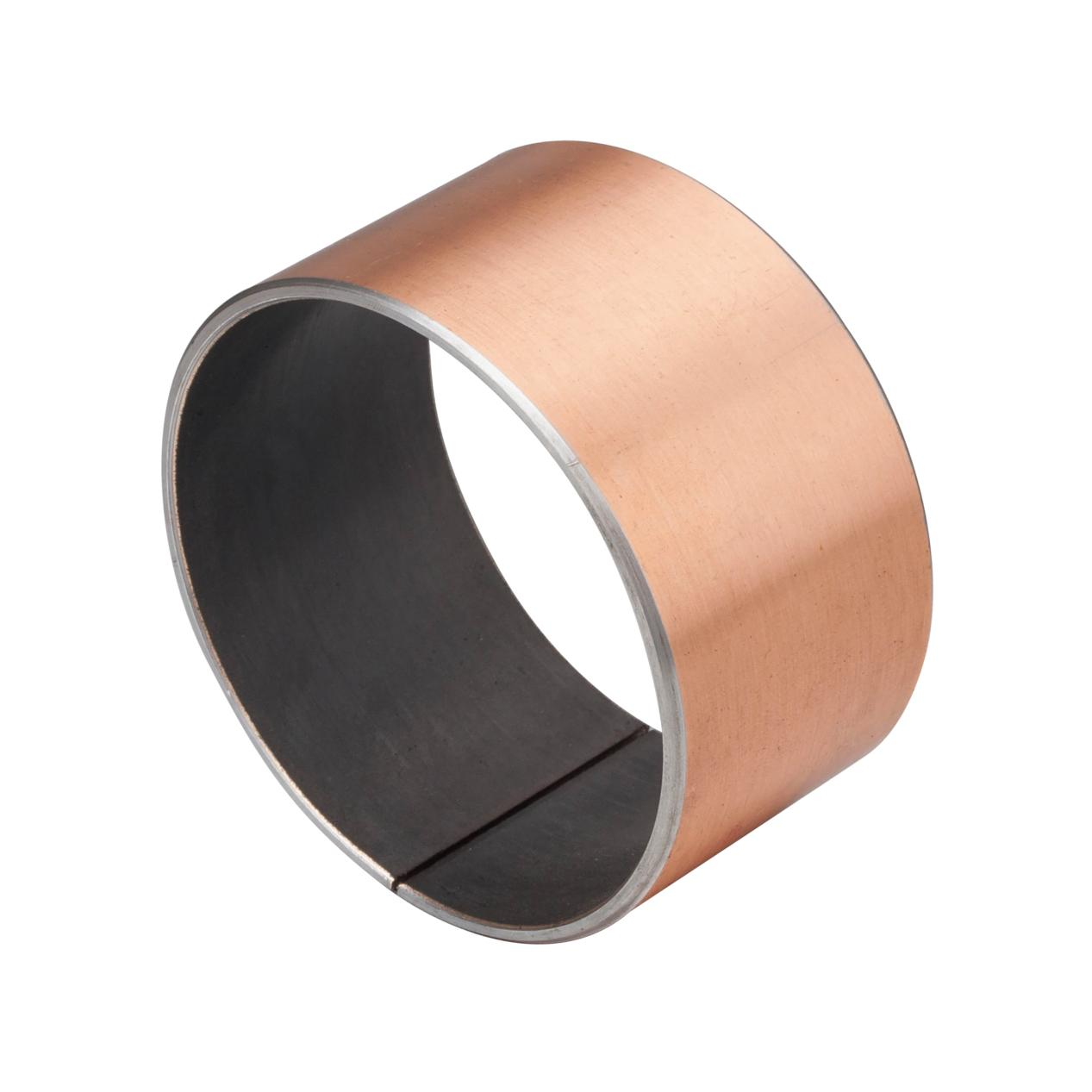
Maintenance-Free SF-1 Self-Lubricating Bearing for Heavy Duty Applications - Low Noise & High Load
The manufacturing process of SF-1 bearings is a precise multi-step procedure. It typically involves:
Sintering: The porous bronze powder is applied to the steel back and then subjected to a high-temperature sintering process. This process bonds the bronze to the steel, creating a strong and integrated structure with controlled porosity.
Impregnation: The sintered bronze layer is then impregnated with the PTFE and filler mixture under controlled conditions, often involving heat and pressure. This ensures that the self-lubricating composite fills the pores completely.
Forming and Finishing: Finally, the material is cut, formed, and machined into the desired bearing shape (bushings, thrust washers, strip, etc.) and precisely sized to meet specific application requirements.
2. Advantages and Disadvantages of SF-1 Oilless Bearing
SF-1 oilless bearings offer a compelling set of advantages, making them a preferred choice in numerous applications, though they do come with certain limitations:
Advantages:
Maintenance-Free, Oil-Free Lubrication: This is the most significant advantage. The integrated self-lubricating layer eliminates the need for external oil or grease lubrication, significantly reducing maintenance costs, eliminating messy oil leaks, and simplifying design.
Low Friction, Wear Resistance: The PTFE-based sliding layer provides an extremely low coefficient of friction, leading to reduced power loss and heat generation. This, coupled with the wear-resistant fillers, results in extended bearing life.
Suitable for High Load, Low Speed or Oscillating Motion: SF-1 bearings excel in applications where traditional liquid lubrication might be squeezed out or where continuous lubrication is difficult to maintain. Their self-lubricating properties ensure consistent performance even under heavy loads, slow speeds, or frequent start-stop operations and oscillating movements.
Compact Design: The absence of external lubrication systems allows for more compact and simplified mechanical designs.
Environmental Friendliness: Eliminating oil and grease contributes to a cleaner working environment and reduces the disposal of hazardous lubricants.
Wide Operating Temperature Range: The robust material composition allows SF-1 bearings to operate effectively across a broad spectrum of temperatures.
Disadvantages:
Limited High-Speed Capability: While suitable for high loads, SF-1 bearings generally have limitations in very high-speed applications due to potential heat buildup from friction that the self-lubricating layer might not dissipate quickly enough.
Sensitivity to Contaminants: Abrasive particles can embed in the PTFE layer, leading to increased wear on the shaft.
Cost: Initial cost can be higher than some traditional bearings, though this is often offset by long-term maintenance savings.
Load Direction Specificity: Some SF-1 variations might have directional load limitations depending on the design and material composition.
3. Application Areas of SF-1 Oilless Bearing
The versatile nature and inherent benefits of SF-1 oilless bearings have led to their widespread adoption across diverse industries:
Automotive Industry: A cornerstone of modern vehicles, SF-1 bearings are found in critical systems such as:
Suspension Systems: Enabling smooth articulation and reducing friction in shock absorbers, control arms, and leaf springs.
Steering Mechanisms: Ensuring precise and effortless steering in steering columns and linkages.
Brake Systems: In various pivot points and linkages.
Pedal Assemblies and Door Hinges: Providing durable and maintenance-free operation.
Industrial Machinery: Their robustness and maintenance-free operation make them ideal for heavy-duty industrial applications:
Conveyors: In rollers and idlers, reducing friction and extending the life of the system.
Hydraulic Equipment: In cylinders, pumps, and valves, where their resistance to various fluids is beneficial.
Packaging Machinery, Textile Machinery, and Agricultural Equipment: Where reliable, continuous operation is paramount.
Household Appliances: Contributing to the longevity and quiet operation of everyday devices:
Washing Machines: In drum supports and agitator mechanisms.
Air Conditioners: In fan motors and damper linkages.
Refrigerators, Dishwashers, and Small Motors: Where low noise and long life are desired.
Special Fields: Beyond conventional industries, SF-1 bearings play a crucial role in specialized applications:
Aerospace: In aircraft landing gear, control surfaces, and interior mechanisms, where reliability and weight savings are critical.
Medical Equipment: In prosthetic joints, hospital beds, and surgical instruments, demanding high precision, cleanliness, and long-term performance.
Office Automation Equipment: In printers, copiers, and shredders.
Renewable Energy: In wind turbine pitch and yaw systems, and solar panel tracking mechanisms.
4. Comparison between SF-1 Oilless Bearing and Traditional Bearings
To fully appreciate the advantages of SF-1 oilless bearings, it's essential to compare them with their traditionally lubricated counterparts:
Lubrication Method:
SF-1 Oilless Bearing: Employs a self-lubricating layer, providing continuous lubrication without external intervention.
Traditional Bearings (e.g., ball bearings, roller bearings, plain bearings): Rely on external lubrication (grease, oil, or even solid lubricants applied externally) to separate moving surfaces, reduce friction, and dissipate heat.
Service Life Comparison:
SF-1 Oilless Bearing: Can offer a comparable or even longer service life in specific applications (high load, low speed, oscillating motion) due to consistent self-lubrication, especially where traditional lubrication might fail or be neglected.
Traditional Bearings: Service life is highly dependent on proper lubrication and maintenance. If lubrication fails, wear accelerates rapidly, leading to premature failure.
Maintenance Cost Comparison:
SF-1 Oilless Bearing: Significantly lower maintenance costs. Eliminates the need for regular re-lubrication, oil changes, grease gun purchases, and associated labor. Reduces downtime for maintenance.
Traditional Bearings: Higher maintenance costs due to regular lubrication schedules, the cost of lubricants, potential for lubricant disposal, and the labor involved in maintenance.
5. Selection and Installation of SF-1 Oilless Bearing
Proper selection and meticulous installation are paramount to maximizing the performance and lifespan of SF-1 oilless bearings:
How to Choose the Right SF-1 Bearing:
Load Capacity: Determine the maximum radial and axial loads the bearing will experience. SF-1 bearings have specific static and dynamic load ratings that must not be exceeded.
PV Value (Pressure-Velocity): This is a critical factor for oilless bearings. It's the product of the bearing pressure (P) and the sliding velocity (V). Each SF-1 bearing material has a maximum allowable PV value. Exceeding this can lead to excessive heat generation and premature wear.
Operating Temperature: Consider the ambient and generated operating temperatures. Ensure the chosen SF-1 material can withstand the temperature range without degradation of its self-lubricating properties.
Speed: While suitable for low to moderate speeds, be mindful of the maximum permissible sliding speed.
Shaft Material and Surface Finish: A smooth, hard shaft surface (e.g., hardened steel with a fine finish of Ra 0.4 to 0.8 µm) is crucial for optimal performance and reduced wear on the bearing's PTFE layer.
Environmental Factors: Account for potential exposure to chemicals, moisture, or abrasive contaminants. Specialized SF-1 variants might be required for aggressive environments.
Dimensional Requirements: Accurately measure the bore diameter, outer diameter, and length to ensure a proper fit.
Installation Precautions:
Cleanliness: Ensure both the bearing and the housing/shaft are thoroughly clean and free of any debris, burrs, or foreign particles before installation. Even small particles can significantly impair performance and life.
Proper Alignment: Maintain accurate alignment between the shaft and the housing bore. Misalignment can lead to uneven load distribution, edge loading, and accelerated wear.
Avoid Overloading: Never exceed the bearing's specified load capacity, especially during installation. Do not hammer or force the bearing into place.
Correct Press Fit: SF-1 bearings are typically installed with an interference (press) fit into the housing. Use appropriate pressing tools or mandrels to apply even pressure to the bearing's outer diameter, ensuring it is seated squarely and without distortion. Avoid pressing on the self-lubricating layer.
Shaft Entry: When inserting the shaft, ensure it is chamfered to prevent damage to the inner self-lubricating layer of the bearing. Use a smooth, controlled motion.
No External Lubrication (Unless Specified): Generally, no external lubrication is required or recommended for SF-1 bearings. Adding grease or oil can sometimes trap contaminants or interfere with the self-lubricating mechanism. However, in dusty environments, a grease seal might be used to prevent ingress of contaminants, but the grease itself should not be intended for bearing lubrication.
Maintenance Recommendations:
Periodic Inspection: Although maintenance-free in terms of lubrication, periodic visual inspection is recommended to check for signs of wear, damage, or contamination.
Cleaning (If Necessary): If exposed to significant dust or debris, light cleaning of the exposed surfaces might be beneficial, but avoid harsh chemicals or abrasive cleaning methods.
Checking Wear: Monitor for any increase in clearance or signs of excessive wear on the inner surface. If significant wear is observed, the bearing may need replacement.
Environmental Control: Where possible, minimize exposure to excessive dust, moisture, or corrosive agents to prolong bearing life.
6. Common Problems and Solutions
Even with proper selection and installation, SF-1 bearings can occasionally encounter issues. Understanding common problems and their solutions can help maintain optimal performance:
Abnormal Noise Problems:
Possible Causes: Contamination (e.g., dirt, grit) between the shaft and the bearing surface; poor shaft surface finish; excessive radial or axial play; misalignment; overloading.
Solutions: Clean the bearing and shaft thoroughly; ensure the shaft has the recommended surface finish; check and correct bearing clearances; re-align the components; verify that the operating loads are within the bearing's capacity.
Possible Causes of Abnormal Wear:
Lack of Sufficient Lubrication (for self-lubricating bearings, this means exceeding PV limits): The PV value (Pressure x Velocity) is too high, leading to excessive heat generation and breakdown of the self-lubricating layer.
Abrasive Contamination: Hard particles entering the bearing interface, scratching both the bearing and the shaft.
Corrosion: Chemical attack on the bearing materials, especially if exposed to aggressive fluids not compatible with the PTFE composite.
Misalignment: Uneven load distribution leading to localized wear.
Edge Loading: Occurs when the load is concentrated at the edges of the bearing, often due to misalignment or shaft deflection.
Poor Shaft Surface Finish: A rough shaft surface acts like a file, abrading the bearing material.
Excessive Temperature: Operation beyond the bearing's maximum temperature limits can degrade the PTFE layer.
Overloading: Consistently exceeding the bearing's static or dynamic load ratings.
Vibration: Excessive vibration can contribute to fretting wear.
Incorrect Material Selection: Using an SF-1 bearing type that is not suited for the specific application's load, speed, or environmental conditions.
How to Extend Service Life:
Adhere to Design Limits: Always operate within the bearing's specified PV value, load limits, and temperature range.
Maintain Shaft Quality: Ensure the shaft is hardened and has the recommended surface finish to minimize wear on the bearing.
Prevent Contamination: Implement seals or protective covers in dusty or abrasive environments.
Ensure Proper Alignment: Accurate alignment during installation and throughout operation is crucial.
Avoid Shock Loads: Design the system to minimize sudden impacts or excessive shock loads.
Choose the Right SF-1 Variant: Select the specific SF-1 material and construction that best matches the application's unique requirements (e.g., for high temperature, specific chemical resistance).
Monitor System Conditions: Regularly check for any changes in noise, temperature, or vibration that might indicate an underlying issue.
SF-1 oilless bearings represent a significant leap forward in bearing technology. Their self-lubricating properties, combined with robust construction, offer a compelling solution for a wide range of applications, contributing to reduced maintenance, increased reliability, and a more sustainable mechanical design landscape. By understanding their characteristics and adhering to best practices for selection and installation, engineers can fully harness the potential of these remarkable components.