Operating in high-temperature environments presents unique challenges for bearing systems, where conventional lubricants degrade rapidly, leading to increased friction and premature failure. Self-lubricating bronze bushings for high-temperature applications provide an effective solution by integrating solid lubricants directly into the bronze matrix, ensuring consistent performance even under extreme thermal conditions.
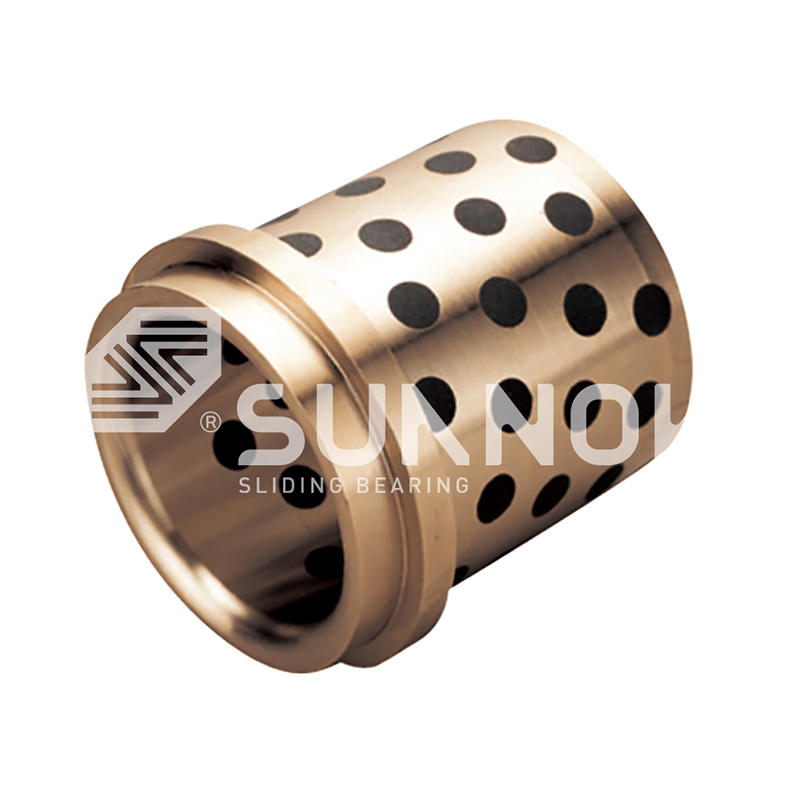
GB61 Copper NAAMS Standard Flanged Solid-lubricating Bearing
The fundamental principle behind these bearings lies in their composite structure, typically consisting of a bronze alloy (such as SAE 841 or C93200) embedded with solid lubricants like graphite, molybdenum disulfide (MoS₂), or a combination of both. Under high temperatures, traditional oil or grease lubricants evaporate or carbonize, but solid lubricants remain stable, continuously releasing lubricating particles at the friction interface. This mechanism significantly reduces wear, even in environments exceeding 260°C (500°F), making them ideal for furnaces, kilns, and heavy industrial machinery.
One critical consideration in high-temperature applications is thermal expansion. Bronze alloys exhibit predictable expansion rates, allowing engineers to calculate precise clearances to prevent seizing at elevated temperatures. Additionally, oxidation resistance is enhanced through alloying elements such as aluminum and nickel, which form protective oxide layers. Comparative studies between standard bronze bearings and self-lubricating bronze bushings for high-temperature applications demonstrate a 3-5x increase in service life when operating above 200°C, primarily due to the elimination of lubricant breakdown.
Real-world applications include steel mill conveyor systems, where bearings must endure both heavy loads and radiant heat. In these settings, graphite-embedded bronze bushings have shown superior performance over traditional roller bearings, which require frequent re-lubrication and cooling. Another example is in industrial gas turbines, where thermal cycling (rapid heating and cooling) demands materials that maintain dimensional stability. Here, MoS₂-infused bronze bearings outperform alternatives by reducing friction-induced heat generation, thereby minimizing thermal stress on adjacent components.
When selecting bearings for extreme heat, engineers must evaluate load capacity, thermal conductivity, and the specific type of solid lubricant used. Graphite excels in oxidizing atmospheres, while MoS₂ performs better in low-oxygen or vacuum environments. Hybrid compositions, incorporating both materials, offer balanced performance for variable conditions. The absence of external lubrication also eliminates contamination risks, a critical factor in food processing or semiconductor manufacturing where cleanliness is paramount.
2. Maintenance-Free Solid-Lubricated Bronze Bearings for Food Processing Equipment
The food and beverage industry imposes stringent requirements on machinery components, particularly regarding hygiene, corrosion resistance, and ease of cleaning. Maintenance-free solid-lubricated bronze bearings for food machinery address these demands by eliminating grease or oil, which can attract contaminants and breed bacteria. These bearings comply with FDA, NSF, and EU food-grade material standards, ensuring safe operation in direct or incidental food contact zones.
A key advantage of solid-lubricated bronze bearings in food applications is their resistance to aggressive cleaning agents, such as chlorine-based sanitizers or high-pressure steam. Traditional lubricated bearings degrade under frequent washdowns, leading to corrosion and increased friction. In contrast, food-grade bronze alloys (e.g., C95400 aluminum bronze) combined with embedded PTFE or graphite provide a non-porous surface that resists chemical attack while maintaining low friction.
Hygienic design principles further enhance performance. Bearings used in meat processing or dairy equipment often feature smooth, crevice-free surfaces to prevent bacterial accumulation. Some advanced designs incorporate antimicrobial coatings, such as silver-ion treatments, to inhibit biofilm formation. These features are critical in conveyor systems, filling machines, and packaging lines, where downtime for cleaning or bearing replacement directly impacts productivity.
Performance comparisons between maintenance-free solid-lubricated bronze bearings for food machinery and polymer-based alternatives reveal distinct trade-offs. While engineering plastics like UHMWPE offer corrosion resistance, they lack the load capacity and thermal conductivity of bronze. In high-load applications, such as dough mixers or canning presses, bronze bearings with solid lubricants sustain longer service life without deformation. Additionally, bronze's higher thermal diffusivity helps dissipate heat generated during continuous operation, reducing the risk of thermal degradation.
Case studies in commercial bakeries demonstrate the economic benefits of these bearings. A switch from grease-lubricated steel bearings to solid-lubricated bronze units reduced maintenance intervals by 70%, while eliminating lubrication-related product contamination. Similarly, in beverage bottling plants, the absence of lubricant leakage prevented sticky residue buildup on conveyor chains, further minimizing downtime.
3. Oil-Free Bronze Bearings with Graphite Plugs for Heavy-Duty Machinery
Heavy-load industrial applications demand bearings that can withstand substantial forces without frequent maintenance. Oil-free bronze bearings with graphite plugs for heavy loads excel in such environments by combining the strength of bronze alloys with the self-lubricating properties of graphite inserts. These bearings are particularly valuable in mining, construction, and agricultural equipment, where external lubrication is impractical.
The design of graphite-plugged bronze bearings involves strategically placed graphite inserts within the bearing's load-bearing surface. Under operational pressure, graphite gradually transfers to the mating surface, forming a protective lubricating film. This process compensates for wear over time, maintaining consistent performance even under dynamic or impact loads. Testing shows that such bearings can sustain PV (Pressure-Velocity) values exceeding 50,000 psi·ft/min, outperforming standard oil-impregnated bronze bearings by 30-40%.
A critical advantage of oil-free bronze bearings with graphite plugs for heavy loads is their ability to operate in contaminated environments. Unlike oil-lubricated bearings, which can fail when exposed to dirt or moisture, graphite-lubricated systems remain functional even with particulate ingress. This makes them ideal for bulldozer pivot points, excavator arm joints, and other off-highway equipment applications where sealing systems often fail.
Comparative analyses between different graphite configurations reveal performance nuances. Bearings with larger, fewer plugs exhibit better initial lubrication but may experience uneven wear. Conversely, designs with numerous small plugs ensure more consistent lubricant distribution but require higher manufacturing precision. Field data from mining draglines indicates that optimized plug patterns can extend bearing life by up to 50% compared to non-plugged bronze bearings under similar loads.
Failure modes in these applications typically involve either graphite depletion or bronze fatigue. Advanced monitoring techniques, such as vibration analysis, can detect early signs of lubrication film breakdown, allowing proactive replacement. Some manufacturers now offer bearings with reserve graphite plugs beneath the surface layer, which become active as the primary plugs wear down, further extending service intervals.
4. Corrosion-Resistant Solid-Lubricating Bronze Bearings for Marine Applications
The marine environment presents one of the most aggressive corrosion scenarios for mechanical components. Corrosion-resistant solid-lubricating bronze bearings for marine use solve this challenge through specialized alloy compositions and innovative lubrication systems that withstand saltwater exposure while maintaining reliable performance.
Marine-grade bronze bearings typically use nickel-aluminum bronze (NAB) alloys, which demonstrate superior corrosion resistance compared to standard tin bronzes. The aluminum content in these alloys forms a passive oxide layer that protects against pitting and crevice corrosion - common failure modes in seawater applications. When combined with solid lubricants like graphite or PTFE, these bearings achieve both corrosion resistance and excellent wear properties, even in submerged conditions.
A key application for corrosion-resistant solid-lubricating bronze bearings for marine use is in ship propulsion systems. Rudder bearings, for instance, must handle high loads while constantly exposed to seawater. Traditional lubricated bearings fail quickly in this environment, but solid-lubricated versions have demonstrated service lives exceeding 10 years in commercial vessels. The absence of external lubrication also eliminates the risk of oil pollution in sensitive marine ecosystems.
Design innovations in marine bearings include channeled surfaces that allow water flow for cooling while preventing sediment accumulation. Some advanced designs incorporate sacrificial anode materials directly into the bearing housing, providing additional cathodic protection. These features are particularly valuable in offshore oil platforms and desalination plants, where maintenance access is limited and component failure can have catastrophic consequences.
Performance testing in simulated marine environments shows that properly specified bronze bearings can withstand salt spray concentrations 5-7 times higher than standard bearings before showing signs of corrosion. The solid lubrication system continues to function even as minor surface corrosion occurs, unlike oil-lubricated systems where corrosion products quickly degrade lubrication effectiveness.
5. PTFE-Coated Bronze Bearings for Dry Running Conditions
In applications where traditional lubricants cannot be used, PTFE-coated bronze bearings for dry running conditions provide an optimal solution by combining the load-bearing capacity of bronze with the ultra-low friction properties of polytetrafluoroethylene. These bearings excel in cleanroom environments, vacuum systems, and other situations where lubricant contamination must be avoided.
The PTFE coating on these bearings works through a unique transfer film mechanism. As the bearing operates, a thin layer of PTFE transfers to the mating surface, creating a self-lubricating interface that reduces friction coefficients to as low as 0.05-0.10. This process occurs without any external lubrication, making these bearings ideal for semiconductor manufacturing equipment, medical devices, and aerospace applications where cleanliness is critical.
Compared to traditional lubricated bearings, PTFE-coated bronze bearings for dry running conditions offer several advantages in specialized environments. In vacuum applications, they eliminate outgassing concerns associated with conventional lubricants. In food processing, they provide lubrication without risk of product contamination. In cryogenic conditions, they maintain performance where oils would solidify or greases would become ineffective.
Material science advancements have led to improved PTFE composite formulations that enhance wear resistance while maintaining low friction properties. Some modern coatings incorporate filler materials like bronze powder or carbon fiber to improve load capacity and thermal conductivity. These developments have expanded the application range of PTFE-coated bearings into more demanding mechanical systems while maintaining their dry-running capabilities.
Case studies in industrial robotics demonstrate the effectiveness of these bearings in high-cycle applications. A typical SCARA robot joint using PTFE-coated bronze bearings can achieve over 50 million cycles without maintenance, compared to just 5-10 million cycles for oil-lubricated alternatives. This dramatic improvement in service life, combined with elimination of lubrication maintenance, makes them increasingly popular in automated manufacturing systems.
6. Technical Considerations and Selection Guidelines
Selecting the appropriate solid-lubricating bronze bearing requires careful analysis of operating conditions and performance requirements. The first consideration should be load characteristics - whether the application involves continuous rotation, oscillating motion, or static loading. Each motion type affects how the solid lubricant is distributed and consumed during operation.
Environmental factors play an equally important role in bearing selection. High-temperature applications favor graphite-embedded designs, while corrosive environments demand specialized alloys like nickel-aluminum bronze. For applications requiring ultra-clean operation, PTFE-coated bearings provide the best solution. Understanding these material-specific advantages ensures optimal bearing performance in each unique application scenario.
Installation and maintenance practices significantly impact bearing lifespan. Proper clearance calculations must account for thermal expansion, especially in high-temperature applications. Bearing housings should be designed to prevent edge loading, which can accelerate wear. While these bearings are marketed as "maintenance-free," periodic inspection for lubricant depletion or abnormal wear patterns can prevent unexpected failures in critical applications.
Emerging technologies in bearing monitoring offer new possibilities for predictive maintenance. Wireless temperature and vibration sensors can track bearing health in real-time, alerting operators to potential issues before catastrophic failure occurs. These advanced monitoring systems are particularly valuable in remote or difficult-to-access installations where unplanned downtime would be especially costly.
Future developments in solid-lubricating bronze bearings may include smart materials that adapt their lubrication properties based on operating conditions, or nano-engineered surface treatments that further reduce friction and wear. As manufacturing technologies advance, we can expect to see bearings with even longer service lives and broader application ranges across industries.