An oilless thrust washer is a specialized bearing component designed to handle axial loads without requiring external lubrication. Unlike traditional thrust washers, which rely on oil or grease, these self-lubricating variants incorporate materials like PTFE, graphite, or bronze composites to reduce friction and wear.
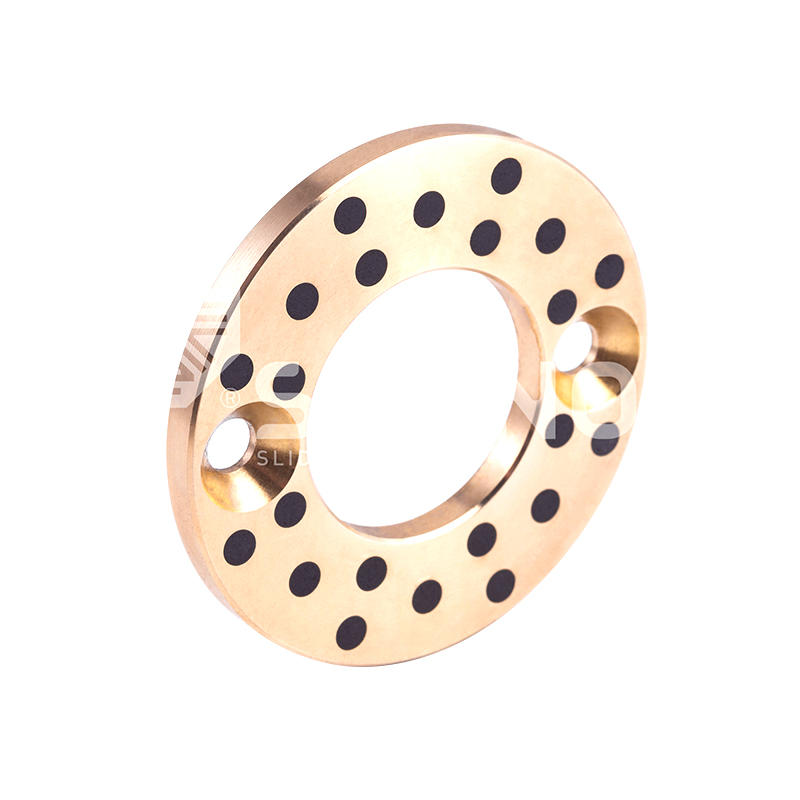
JTW Solid Lubricant Graphite Oilless Bronze Thrust Washer Bearing
Working Mechanism
The operational principle involves embedded solid lubricants that form a low-friction film during rotation. This eliminates the need for oil reservoirs or frequent re-greasing, making them ideal for...
Key Structural Components
- Base material (steel, bronze, or polymer)
- Solid lubricant impregnation
- Load-bearing surface pattern
- Thermal expansion compensation layer
Top 5 Applications of Maintenance-Free Thrust Washers
Maintenance-free thrust washers excel in environments where lubrication is impractical or contaminating. Below are critical use cases:
Industrial Machinery
In conveyor systems, these washers prevent material contamination in food processing plants. Compared to lubricated alternatives, they reduce downtime by 30-40% in dusty environments.
Automotive Systems
Electric vehicle transmissions increasingly adopt them to avoid oil leakage risks. A comparison of performance metrics:
Parameter |
Oilless Washer |
Lubricated Washer |
Service Life |
15,000-20,000 hrs |
10,000-12,000 hrs |
Temp Range |
-40°C to +250°C |
-20°C to +150°C |
Selecting self-lubricating thrust bearings requires evaluating four critical factors:
Load Capacity Requirements
Dynamic vs. static load ratings must align with operational stresses. Polymer-based washers typically handle 10-15% higher shock loads than metallic variants.
Environmental Conditions
- Chemical exposure limits material choices
- Humidity affects certain lubricant matrices
- Particulate contamination risks
Performance Comparison: Dry-Running Thrust Washers vs Traditional Options
Dry-running thrust washers demonstrate distinct advantages in specific scenarios:
Friction Characteristics
Testing data shows coefficient of friction values:
Speed (RPM) |
Oilless Washer (μ) |
Greased Washer (μ) |
500 |
0.08-0.12 |
0.05-0.07 |
2000 |
0.10-0.15 |
0.12-0.18 |
Maintenance Requirements
Eliminating lubrication schedules reduces labor costs by approximately 25 man-hours annually per machine in heavy industries.
Installation Best Practices for PTFE-Coated Thrust Washers
Proper installation of PTFE-coated thrust washers ensures optimal performance:
Surface Preparation
- Clean mating surfaces with non-residue solvents
- Verify shaft/housing roundness (max 0.002" TIR)
- Deburr all edges
Mounting Procedures
Unlike oil-impregnated washers, PTFE variants require no break-in period but need precise axial alignment. Misalignment exceeding 0.5° can reduce lifespan by 60%.
Long-Term Reliability Factors for Graphite-Embedded Thrust Plates
Graphite-embedded thrust plates offer unique longevity benefits:
Wear Mechanism Analysis
The graphite release rate is engineered to match expected wear patterns. Accelerated testing shows:
Operating Hours |
Wear Depth (Microns) |
1,000 |
2-3 |
10,000 |
15-18 |
Failure Mode Prevention
Common issues like lubricant starvation or thermal degradation are inherently avoided, though overload scenarios still require consideration.